
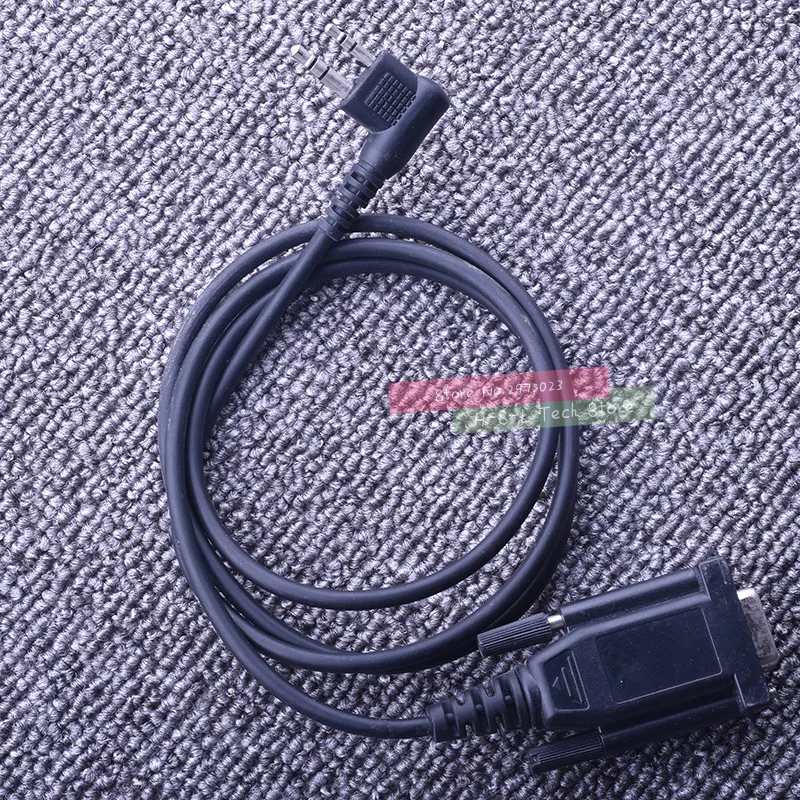
The reason we say “pseudo” is that a push button doesn’t contain a transistor and is simply driving the voltage High or Low. Furthermore, a simple pushbutton may be wired to be a pseudo PNP or NPN device. However, the datasheet of the PLC provides a comprehensive diagram. This concept is often missunderstood by engineers and technicians. The PLC inputs may be configured as sourcing or sinking. Since we’re only using push buttons for this example, we only need to worry about the inputs. The L24ER-QB1B PLC is equipped with Inputs and Outputs directly on the main hardware. We will be adding a start and stop push buttons to control our drive through some basic ladder logic. Now that the PowerFlex 525 VFD is controlled through EtherNet/IP, we need to add external controls to our PLC. Wiring Start Stop Push Buttons into CompactLogix Allen Bradley PLC

This is a required step in order for the drive to set the parameters we’ve given it in the previous steps. Therefore, we must start with the following:īy setting this parameter to 4, the module is reset without affecting the memory of the drive. However, the drive may take an IP address setting from Rockwell’s BOOTP Utility or the parameters. Controlling PowerFlex 525 Drives over EtherNet IPĮstablishing EtherNet IP connectivity to a PowerFlex 525 drive requires us to set the IP address and the subnet mask. As the names suggest, parameters within a section will address the setup of electrical parameters, communication with other devices, logical programming and the display of the drive. These parameters are split into six sections:Įach section has specific parameters for the drive. Within the datasheet, you’ll find parameters which may be configured to suit a specific application. If you’re planning on using pushbuttons, the jumper must be removed. This jumper needs to be in place while the drive is controlled over EtherNet/IP. Note that there’s a pre-installed jumper between terminals 01 and 11. This includes wiring diagrams as well as parameters which we will be setting up shortly. Within the datasheet, the user will find a lot of information about the setup of the drive. PowerFlex 525 Variable Frequency Drive Basic Wiring and Parameters
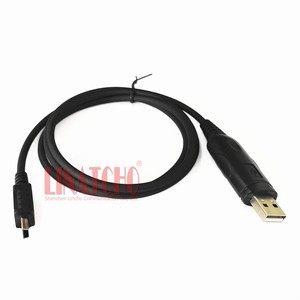
Hyt tc 500 programming cable diagram how to#
In this tutorial, we’ll take a look at how to integrate a PowerFlex 525 VFD into RSLogix Studio 5000 over EtherNet IP. By doing so, the programmer is able to create advanced motion routines in addition to the simple start and stop features. However, a much more practical approach is to add the drive to a private network which includes a Programmable Logic Controller. These drives can be easily wired to start and stop from push buttons through direct inputs. Their reliability as well as ease of use, especially within the Rockwell Automation ecosystem, has allowed them to become popular all over the world.Ĭomissioning a PowerFlex 525 VFD is straightforward.
Hyt tc 500 programming cable diagram series#
The PowerFlex 525 series of Variable Frequency Drives from Allen Bradley are an excellent choice & have been an industry standard for several years. VFDs are flexible, provide additional control and data in every application. Based on this phenomenon, it’s now recommended to utilize a VFD over a contactor in every application. Over the last decade, these devices have become increasingly cheaper. Variable Frequency Drives are used within the automation industry to drive induction motors with added precision over a simple contactor.
